It looks a little like magic: When a crack forms in this new concrete, the material begins to fill in the gap itself. The process uses an enzyme found in red blood cells to make one of the most ubiquitous materials on the planet much more durable—and help shrink the concrete industry’s giant carbon footprint.
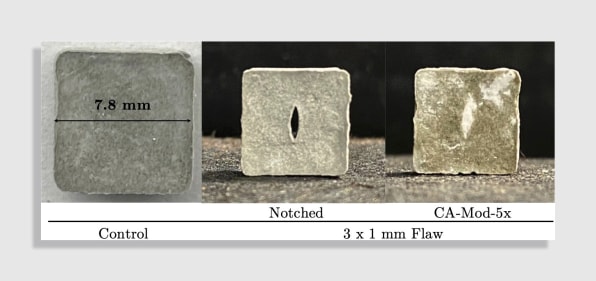
“Concrete production and repair and transport is a very, very, energy-intensive problem,” says Nima Rahbar, an associate professor of civil and environmental engineering at Worcester Polytechnic Institute, who led the development of the new technology. By one recent estimate, the material is responsible for around 9% of global CO2 emissions, more than three times more than the airline industry. If the industry was a country, it would be the third largest climate polluter in the world. While some startups work on making concrete differently, the new technology can help by shrinking overall demand. “If you can make concrete that can last longer, so you don’t have to replace it, you can make a dent in this 9% of emissions,” he says.
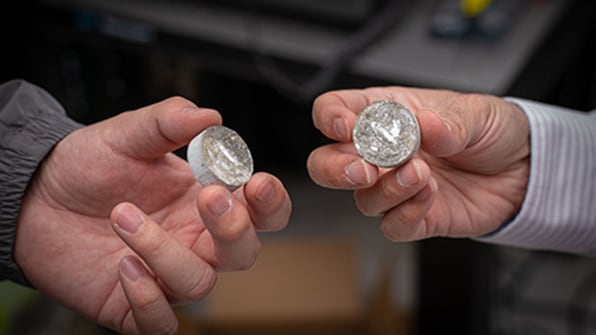
Some earlier experimental self-healing concrete used bacteria to make repairs, but the process is slow. “It’s not really pragmatic to fix this stuff in a reasonable timeframe,” says Rahbar. Bacteria are also expensive and could pose safety issues. He started to look for an alternative, and took inspiration from how the human body processes CO2. “We inhale oxygen and we exhale CO2,” he says. “So the process of CO2 transport from cells to blood vessels has to be done really quickly.”
A biochemist collaborator, Suzanna Scarlata, suggested using carbonic anhydrase, the same enzyme that transfers CO2 from cells into the blood stream. When the enzyme is added to concrete powder, it helps the material turn CO2 in the atmosphere into calcium carbonate crystals. Whenever a tiny crack forms, the calcium carbonate fills it in. A millimeter-scale crack can be filled within a day, preventing larger cracks from forming. A similar process can also be used on cracks in traditional concrete. “We spray a solution that is composed of enzyme, water and calcium,” Rahbar says. “We then can blow CO2 and fill the cracks in minutes, or use ambient CO2 that will take longer to heal the cracks.”
carbon-negative concrete, concrete recycling, enzymatic corrosion inhibitor, GCCA, Innovandi Open Challenge